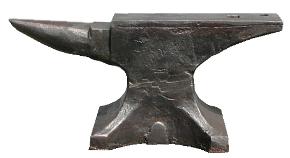
"Real" blacksmiths anvils are solid metal, either faced with tool steel, made partially of tool steel or entirely of tool steel.
"Real" blacksmiths anvils follow certain conventions of shape that have developed over thousands of years but there are anvils used by many other craftsfolk and specialists that do not necessarily follow these conventions.
The purpose of a blacksmiths' anvil is to support hot and cold work and resist the blows of heavy hammers without moving, chipping or breaking.
The best blacksmiths anvils have a number of similar features but they do not all have the same overal shape.
These nearly universal features include:
- A mass 50 times greater than the heaviest hand hammer the smith will use on the anvil.
- Flat hard face (however the Chineses prefer a highly crowned face)
- A curved surface to make smooth bends over, usualy semi-conical, bird beak or rhinoceros horn shaped.
- A square "hardie" hole to support hardies and other tools.
- One or more round holes for punching.
Blacksmith anvils can have other features as well but the above are generally considered the minimum.
Other features include
a tapered square horn (making it a double horn anvil), side shelves and side horns, side "clip horns", upsetting blocks, toggles and extra hardie and pritichell holes.
The earliest anvils were stone. The earliest metal anvils were cast bronze.
For millinea blacksmiths' anvils were forged wrought iron and steel.
Most good modern anvils are a high grade cast steel that can be hardened and tempered to 52 to 56 HRc.
In either case the making of anvils was and is an industrial process.
Necessary Tools
Making anvils in the small shop is heavy metal sculpture.
It is done with cutting torches, arc welders, heavy hand grinders and LOTS of abrasives.
When available large and small machine tools are used or their services hired.
IF one is stubborn enough and has a large block of steel an anvil can be carved out of the solid just like a sculpture from stone.
In fact it can be done with hammer and chisel and a LOT of time.
This method is terribly wasteful as is most sculpture from the solid.
With skill and the right machinery an anvil can be carved from a large block of steel more efficiently but it is still very wasteful of ever more expensive steel.
Assembly Method
SO, that leaves the build up method. This is the oldest method of making wrought iron anvils.
Blocks of wrought iron similar in size and shape to new pieces of modeling clay were heated and forge welded together until the desired shape was needed.
This takes lots of fuel and man power.
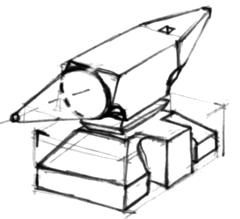
More efficient methods were developed until forged anvils were just two pieces, a top and a bottom first forge welded and then later arc welded at the waist.
This is the method currently used by Peddinghaus, the last maker of forged steel anvils.
This method could still be used to make a very nice fabricated anvil (as shown at right).
Between welding two incredibly heavy heavy pieces together and welding lots of little blocks together by an archaic method there is the middle ground of arc welding small pieces together.
IF the welds are not two numerous and properly designed the end result can be a very satisfactory anvil.
Style or Art:
We have mentioned making an anvil as heavy iron sculpture. Anvils have been and can be art.
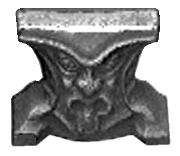
If you are going to put money and effort into making something then you should also put some thought into the design as a piece of art.
Anvils can be plain or ornate, symmetrically balanced or asmetrical, it can be masuline or feminine.
No matter what your taste the design should be strong and well proportioned.
Anvils can also be whimsical as seen in the many Road-Runner cartoons and still symbolize mass and strength.
Skills:
Besides the tools and the materials you need certain skills.
While a hand held cutting torch will cut through up to 6" or more of steel it is VERY difficult to make a cut clean enough that an exorbitant amount of labor will not be necessary to clean up.
Smooth hand flame cutting is a skill that takes much practice.
If your plan calls for a lot of flame cutting you need to find ways to do it by machine cutting.
When possible, sawing is much preffered.
The Upturned Horn, Anthropomorphism
Normally the horns on all well designed anvils with soft iron (wrought or low carbon steel) horns slope upwards about the amount of the step in a straight line from the step to the tip of the horn.
This is so that during the life of the anvil the pounding on the horn that would make it sag,
first goes from up slope (new), to level, then to down slope (old tired).
This increases the visual life of the anvil.
A down slope doesn't hurt mechanically but to the human eye that equates health, youth and vigor with erect anatomical parts an upward slope or even level horn looks better than one that slopes downward or droops.
The anvil is just one of many mechanical things that man has imbued with anthropomorphism.
The "face" and "hands" of a clock, "jaws" of a vise or pliers, the "eyes, nose and mouth" grill of many automobiles and trucks.
Humanoid robots are the ultimate in anthropomorphism.
An anvil has a face, heel, body, waist and feet as well as biological symmetry.
The horn which developed over time to a stylized yet organic looking rhinoceros horn is often considered a phallic device as in "mine's bigger than yours", but could also be recognizably albeit distrotedly female
(From a Western point of view. See African fertility sculpture for another viewpoint).
Modern all-steel anvils have less trouble with sag than the old wrought anvils and many today are made with the horn level, especially when there is no step.
The exception is those designed by connoisseurs of anvil design that understand these details even if they have not analyzed the art or psychology of anthropomorphism.
-guru 02/18/09
Concrete and Anvils
This is a sore subject with the "guru".
When anvilfire was only a few months old a fellow wrote off-line about his concrete anvil.
It was an old concrete post with a cap attached to it and a wide bar of steel for the work surface.
The fellow was so full of himself that I didn't argue the point and said, "It'll work" and then suggested a number of other methods that I indicated were MUCH better.
The next thing you know the fellow was advertising concrete anvils with steel tops at real anvil prices quoting "the guru" that IT WILL WORK. . .
The quote was taken out of context nor did he have my permission to endorse his scheme. We had some heated public discussions about his concrete anvils.
So, here are the problems.
- Concrete is less than 1/3 as dense as steel.
- Concrete is less than 1/100th the strength of steel.
- Concrete shrinks and loses weight over time.
- Concrete spalls (explodes) when exposed to high heats.
SO, while filling a hollow box with concrete may seem like a good way to make an anvil it is not.
It does not weigh very much unless a LOT of it is involved.
The concrete immediately under the steel will start to seperate and crumble fairly soon under heavy use.
AND even if it doesn't loosen from use it will eventually shrink and become loose.
There ARE good points to concrete. It is cheap and easy to use and it deadens noise.
There are methods that improve its usefulness if you insist on using it.
Methods of using concrete:
A concrete filled anvil does little other than reduce noise until the concrete shrinks and comes loose.
However, concrete could be used to fill a base that is integral to an anvil or for machine bases such as for a
power hammer.
One builder used a
concrete inertia block in his anvil stand to reduce vibration and ringing.
Concrete is 60 to 75 percent aggregate (sand and gravel), 10 to 15 percent portland cement and 15 to 20 percent water which becomes part of the concrete.
The higher the aggregate percentage the less shrinkage but the harder the concrete is to place properly.
About 41% of concrete is the larger agregate (crushed stone).
This can be replaced with scrap iron pieces, notably old nuts and bolts.
Replacing all the heavy agregate with iron increases the density of the concrete by almost 100% doubling its weight.
However, this may also weaken the concrete.
Anchorage of the concrete in the steel shell is critical.
Do not count on it sticking to the metal indefinitely.
Ribs perpendicular to the forces on the concrete (horizontal ribs) can improve the grip of the concrete in the steel shell.
A network of re-bar welded to the inside of the shell or framework increases the mass and grip of the concrete in the shell or framework as well as strengthing the concrete.
Both ribs and rebar are better for larger volumes but may apply to smaller ones in some cases.
References and Links
städ, incus, aambeeld, batente